Retaining Walls: Types, Designs, and Functions
Retaining walls are a versatile tool for geotechnical engineers, enabling construction on or along slopes and on sites with limited space in towns and cities.
They come in all types, shapes and sizes – from simple gravity retaining walls to bored pile walls for basements and earth retaining walls using geogrids – to suit a wide range of project needs, and site conditions.
This guide offers a comprehensive introduction to retaining walls. Along the way, we’ll take a closer look at the different types of retaining walls available as well as how they work, the methods of reinforcement, and what to consider in retaining wall designs.
Use the links below to navigate to the sections you are most interested in:
- What is a retaining wall?
- What is the purpose of a retaining wall?
- How do retaining walls work?
- What are the different types of retaining walls?
- The benefits of geogrid reinforced soil walls
- Choosing the right retaining wall
- Design guidance and considerations for retaining wall construction
- Designing retaining walls with TensarTech wall and slope systems
What is a retaining wall?
A retaining wall is a wall that holds back earth or water on one side of it. Above ground, retaining walls are vertical, or near-vertical, structures designed to create level areas on sloping sites.
Retaining walls systems are used in geotechnical engineering primarily to reinforce soil, increase its bearing capacity and increase the soil’s resistance to differential settlement.
What is the purpose of a retaining wall?
Retaining walls are designed to create level areas on sloping sites, to provide additional support to natural slopes at risk of failure and to help maximise development space, creating terraces for infrastructure to run along slopes. They also help to form the walls of basements, underground car parks and metro stations, in towns and cities.
How do retaining walls work?
Retaining walls are designed to restrain soil, or engineering fill, at an angle steeper than the material’s angle of repose – the steepest angle it can hold naturally, without failing. To do this, they need to be able to withstand the horizontal – or lateral – earth pressure, exerted by the material being retained.
Lateral earth pressure is dependent on the vertical stress imposed by the material behind the wall, which is a function of the height of the backfill and its density. It follows then, that the greatest lateral earth pressure is exerted at the base of the wall, because the deeper the backfill, the higher the vertical stress. We’ll explore the effect of lateral earth pressure on retaining walls in more depth further along in this article.
What are the different types of retaining walls?
Retaining walls come in all types, shapes and sizes, from simple gravity walls to bored pile walls for basements and earth retaining walls using geogrids. Each type is designed to suit the specific needs of a project according to the site conditions.
The four main types of retaining walls are gravity retaining walls, cantilever retaining walls, embedded retaining walls, and reinforced soil retaining walls.
The types of retaining walls you should choose for your project depend on a number of different factors. We’ll take a closer look at each of these below.
Gravity retaining walls
Gravity retaining walls use the gravitational force of their own weight to resist the lateral earth pressure from the soil behind them, which prevents toppling and sliding. They are the simplest and earliest recorded type of retaining wall.
Built of concrete, masonry, brick, blocks or mass cast-in-situ concrete, these hard-wearing structures rely on their large weight to resist toppling and sliding caused by the lateral earth pressure from the soil behind them.
Gravity retaining walls are typically designed to be wider at their base, with sloped faces, enabling them to resist the higher lateral earth pressures at depth. As such, this type of retaining wall is easy to build and suitable for retained heights of up to about 3m.
Despite their advantages, gravity retaining walls are not suitable for retained hights above 3m. If built any higher, the retaining structures tend to take up too much space and can end up being too heavy for the ground below, leading to bearing capacity failure. Ultimately, this can result in the wall failing to retain soil.
Cantilever retaining walls
Cantilever walls are built using reinforced concrete, with an L-shaped, or inverted T-shaped, foundation. This kind of retaining wall consists of a stem and a base slab (or footing) which sits under the backfill. The vertical stress behind the wall is transferred onto the foundation, preventing toppling due to lateral earth pressure from the same soil mass, allowing cantilever walls to stand unobstructed.
Additionally, a T-shaped foundation benefits from the weight of soil (and therefore vertical stress) in front of the wall, providing further stability to the retaining structure. Foundations sometimes include a ‘key’ in their base, which sticks into the ground to prevent sliding failure.
A big advantage of cantilever walls compared to other retaining wall types is that they take up little space once built, and are suitable for retained heights of up to 5m. However, construction does require space behind the wall, so these retaining walls are not particularly suited to supporting existing slopes unless temporary support is provided during construction.
Embedded retaining walls
Embedded retaining walls extend deeper than the excavation to take advantage of the passive earth pressure of the ground below. In some cases, embedded walls can extend to 40m deep. This type of retaining wall is used to form near-surface underground structures, such as basements, car parks and metro stations.
Embedded retaining walls work by counteracting the active earth pressure being exerted on the wall above. Additional support is provided to these retaining structures by internal propping – usually from the base slab, ground slab and any intermediate floor slabs – or by ground anchors installed through the wall.
They can be built using a number of different methods, depending on ground conditions, how watertight the excavation has to be, constructability (i.e. time, cost and excavation method) and the retained depth required.
Various types of pile foundations can be used to support retaining walls. For deep excavations, methods include diaphragm walls and panels, as well as bored concrete piles, where piles are either interlocking (secant) or installed next to one another (contiguous). For shallow and temporary excavations, sheet piles and king post walls are commonly used, as shown in the image above.
Reinforced soil, or mechanically stabilised earth, retaining walls
Reinforced soil retaining walls, sometimes referred to as mechanically stabilised earth walls, are constructed using layers of geogrid to reinforce the soil into a stabilised mass. This increases the bearing capacity of the retaining structure, along with its resistance to differential settlement.
Reinforced soil structures have lower bearing pressures, which can eliminate the need for expensive foundations. Instead, geogrids are mechanically connected to a range of facings, including precast concrete blocks and panels, gabions and crib walls, depending on the aesthetic requirements of the project.
Examples of this type of solution include the soil-retaining mesh TR2 system, as well as rock fill gabion-faced and modular block-faced such as our TW1, TW3, and Mesa Wall Systems. For a more organic aesthetic, explore our NaturalGreen™ Slope and GreenSlope Systems.
The benefits of geogrid reinforced soil walls
Load-bearing reinforced soil walls can cut construction costs by up to 75% and halve build times when compared with traditional retaining wall types.
A big advantage of using geogrids, particularly the HDPE geogrid manufactured by Tensar, is that they
work with a huge range of materials. This opens up the possibility of using marginal fill (including selected site-won fill) and waste products such as pulverised fuel ash (PFA). This is a great way to reduce the environmental impact of retaining walls; plus it can save time and money.
Reinforced soil is becoming a standard way of forming cost-effective walls and bridge abutments on roads and railways, instead of the more traditional options that frequently involve piling and reinforced concrete.
Aesthetics
It will be possible to select a type of retaining wall structure that will be sympathetic to the location and enhance the local environment where appropriate.
Here are a few questions you can ask yourself in regards to aesthetics when choosing a retaining wall:
- What is appropriate for the location and environment?
- Are there adjacent structures or features that need to be considered?
- Is the new structure going to be prominent and highly visible to the public?
- Would a green-faced (vegetated) structure enhance the local environment or be out of place?
- Would a high vertical structure be intimidating to pedestrians as opposed to a stepped face or steeply sloping one?
Design life and durability
Designing the structure to meet the required service life, and considering the durability of all components is of course crucial. Certification of systems by recognised bodies such as the British Board of Agrément (BBA) can provide valuable confirmation of the suitability of methods and materials.
Here are a few questions you can ask yourself in regards to design life when choosing a retaining wall:
- How long must the retaining wall last?
- Are all components sufficiently durable?
- What level of inspection and maintenance is appropriate and likely to be provided throughout the life of the structure?
- How will the structure eventually be dismantled and disposed of with minimum disruption and cost?
- If the structure is temporary, has the design fully recognised this to deliver minimum costs (both construction and removal)?
- Is the structure exposed to vandalism and graffiti?
Available space for construction
By carefully examining site-specific constraints and the best use of space. A retaining wall solution can be adopted that best meets the needs of all stakeholders.
Here are a few questions you can ask yourself in regards to footprint when choosing a retaining wall:
- What are the space constraints – during construction and for the completed structure?
- Is there an economic or practical benefit to be gained by minimising the footprint or area taken by the structure?
- Is there sufficient space to enable the use of a steep slope at a lower cost than a vertical wall?
- Is there space for a crane and larger plant during construction or is access an issue – favouring solutions that require only smaller plant and equipment?
- Is the structure supporting an embankment or an excavation – is over-excavation possible to facilitate the construction of certain structure types?
Geotechnical considerations
Clearly, adequate geotechnical information is crucial to developing the most appropriate and cost-efficient retaining wall design.
Here are a few questions you can ask yourself in regards to the geotechnical considerations when choosing a retaining wall:
- What are the foundation soil conditions?
- Piled foundations may be needed for certain structure types – is this cost-effective and can it be avoided?
- Is groundwater going to be an issue - how will this be dealt with?
- Are there suitable structural fill materials available within the site or locally from recycled materials – can these be utilised?
Budgetary constraints
Generally, steep slope structures can be built at a lower cost than vertical walls. Structures requiring piled or rigid foundations are more costly than those requiring no foundation.
Hard-faced structures using concrete or masonry are more expensive to build than green-faced or flexible-faced structures. However, depending on the type and location, some level of maintenance may be required for green-faced structures so this should be taken into account.
The construction cost of different retaining wall solutions varies widely, and it's important to examine the alternatives and determine the most appropriate lifetime cost that meets all the above constraints and considerations.
Design guidance and considerations for retaining wall construction
Whilst a retaining wall is designed to withstand the active earth pressure, without proper analysis and careful design consideration, the structure might fail. To avoid failure of the retaining wall there are some other considerations you should take into account including the presence of groundwater, the ground-bearing capacity and sliding resistance.
Lateral earth pressure
If lateral earth pressure increases to a point where it is higher than the wall can resist, it can cause the wall to topple or overturn. For this reason, when designing retaining walls, engineers must analyse the lateral earth pressure and factor this into their plans.
Types of lateral earth pressure:
Engineers are interested in three types of lateral earth pressure in relation to retaining walls:
- Earth pressure at rest: When the wall is ‘at rest’ and the backfill has not experienced significant post-construction movements.
- Active earth pressure: If the wall moves away from the backfill, the lateral earth pressure falls until it reaches a minimum. This is the active earth pressure – beyond that point, failure will occur.
- Passive earth pressure: If the wall moves into the backfill, pressure increases until it reaches a maximum value, equal to the maximum resistance of the soil – this is the passive earth pressure. In embedded walls, typically used for basements, passive earth pressure is an important factor in stability.
Groundwater and pore pressure
Groundwater is a key design consideration, as it is one of the main causes of retaining wall failure, particularly when using compacted clay fill.
Clay fill compacted to a normal earthworks specification is likely to have negative pore pressure up to considerable heights. Pore pressures are only likely to become positive at the base of very high structures (more than 10m to 15m high), or at lower heights if the clay is on the wet side and therefore soft during placement. If groundwater levels rise behind the wall, pressure can increase beyond what the wall was designed to retain.
Internal slope drainage must let water drain out and must not let water in. It should be designed to intercept groundwater flow and be free-draining, allowing water to drain out easily. It should also not ‘daylight’ at the upper surface of the structure, preventing run-off from flowing into the fill (run-off should be handled by surface water drains, to avoid ponding).
Suction is typically ignored in design and so provides an additional margin against failure or poor performance of the structure. Any movement of a soil structure has the potential to disrupt, or even reverse, the fall of a drain, which could result in water flowing back in – something worth considering when specifying maintenance regimes.
As a result, it is a good idea to maintain suction in the long term and include drainage to allow the free flow of water to prevent pressure build-up.
Ground-bearing capacity
Ground-bearing pressure is an important consideration to ensure the ground below has the capacity to withstand the wall structure. Failure to calculate the bearing capacity of the soil can result in excessive settlement or failure of the ground beneath the wall.
Sliding resistance
If there is insufficient friction (or sliding resistance) at the base of the wall, this can cause the wall to slide, resulting in failure, which can lead to landlsides. As mentioned previously, cantilever retaining walls can be constructed with a T-shaped foundation, including a ‘key’ in their base. This key can help to prevent sliding failure by bearing laterally against the soil, extending passive pressure deeper into the earth beneath.
A retaining wall can have a design life of 100 years, or up to 120 years if incorporating Tensar geogrids. As well as considering the above factors, it is also important to consider any future plans for the site. For example, if something will be built on the ground above the wall after its construction, the design needs to account for a higher vertical stress, and therefore higher lateral earth pressures, to ensure the retaining wall remains stable.
Designing retaining walls with TensarTech wall and slope systems
With 30 years of construction knowledge, design experience and innovative geogrid products, Tensar’s TensarTech permanent and temporary retaining wall systems provide a number of facing types and construction options to suit the structure’s end use, location and required design life.
There is a earth retaining wall for various applications depending on your unique requirements. Our retaining wall solutions include precast concrete, dry-laid modular block systems (with the option of adding architectural, masonry or brick finishes); precast concrete panel systems; gabion and crib walls; and robust units suitable for aggressive marine environments. Our solutions can create vegetated slopes with angles of up to 70˚.
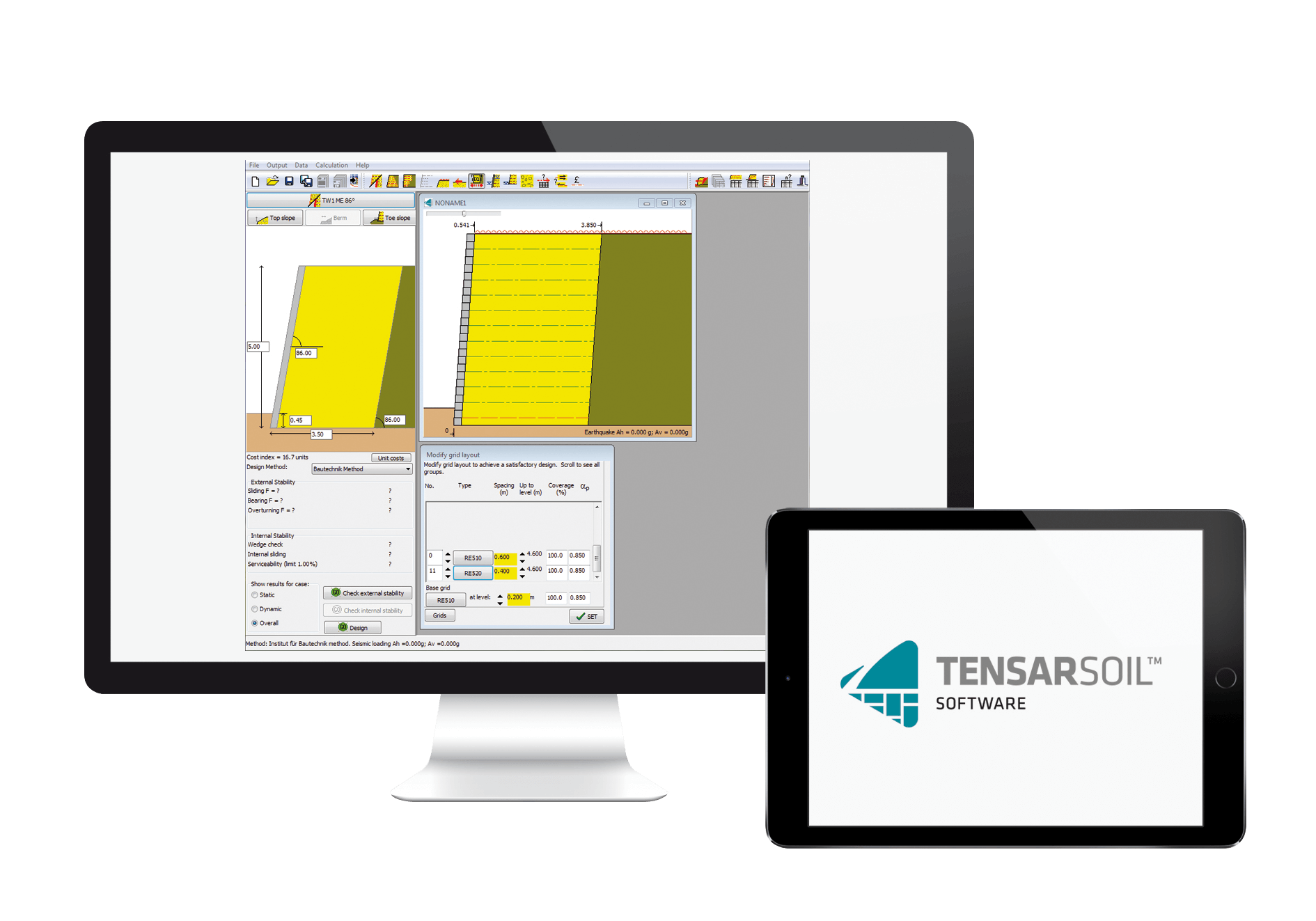