There are a wide range of railway geotechnical engineering issues influencing the construction and maintenance of rail infrastructure. All railways are built upon, cut into, or tunnel through soil and rock. Rail embankments are constructed from natural soils and track foundations constructed from natural aggregates. The condition and properties of these materials will influence the construction process and lifetime performance of a railway.
Where the original geotechnical design is inadequate, major problems arise. This could be a result of incorrect or incomplete knowledge, changing soil conditions due to climate change effects, or increased loading. As a result, railway companies all around the world face expensive and disruptive earthworks repairs, repeated track maintenance, or reconstruction. In many cases line speed restrictions remain in place, caused by poor track geometry and misaligned rails. Disruption of this nature impacts passengers and train operators, as well as the network owners.
To mitigate this, a growing number of railway companies around the globe are incorporating geosynthetic solutions into their infrastructure to address geotechnical problems, both during the initial construction and in renewal and maintenance works. In this guide, we shall explore what these solutions are, the areas in which they are applied, and the numerous benefits they have.
Tensar has developed geogrid solutions that address a number of geotechnical issues in railway engineering. These include railway trackbed stabilisation, foundations for embankments over weak soils, reinforced soil bridge abutments, and steepened embankments.
Looking for something in particular? If so, use the links below, otherwise let’s jump straight in!
- Geotechnical challenges faced in railway design, construction, and maintenance
- Incorporating stabilisation geogrids into trackbed layers to improve performance
- Solutions for railway embankments
- Reinforced soil structures for railways
- Efficiency in design and construction of temporary works that support railway infrastructure projects
- The Tensar difference
Already keen to get started using geotechnical solutions for more durable and sustainable railway construction projects?
Get in touch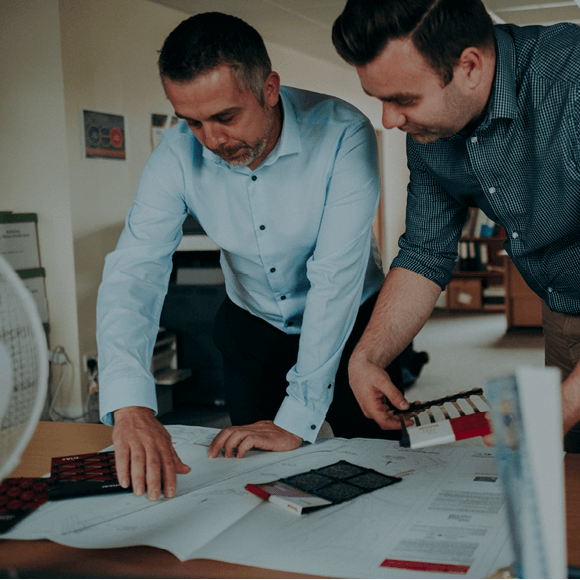
Geotechnical challenges faced in railway design, construction, and maintenance
Designing and building safer, better, longer-lasting railways that are more economical, sustainable, and resilient to changing environmental conditions is the top priority for rail engineers. Rail authorities challenged with maintaining existing rail networks are facing a widening gap between the maintenance needs of a deteriorating network and working with tighter budgets, in addition to addressing the critical challenge of addressing climate change and meeting carbon emission targets. As a result, they require solutions that offer greater resilience and require less frequent and disruptive maintenance.
Railway infrastructure, like all infrastructure works, starts at the ground. Railway geotechnical engineers have to address a multitude of issues. Unlike roads, railways need to avoid steep gradients. This requires more extensive earthworks, deeper cuttings through soil and rock, and higher embankments to maintain an acceptable vertical alignment. River and road crossings require major engineering works - bridges, viaducts, and tunnels. Each of these presents geotechnical challenges.
Above the earthworks or ground level, the trackbed foundation presents railway geotechnical engineers with a set of challenges: bearing capacity, settlement, and drainage all have to be addressed. The foundation soil parameters and the trackbed layer material properties at the time of construction must be understood and accounted for, alongside their potential to change during the life of the railway.
We will cover many of these railway geotechnical issues in this article, but let’s start with the trackbed.
Andrew visits Vietnam's famous Hanoi Railway to talk about the different components of a railway trackbed
Railway trackbed geotechnical issues
Conventionally, railway tracks are a combination of rails and sleepers that are supported by layers of ballast and sub-ballast above the subgrade. Rails on high speed lines are sometimes constructed on a concrete base with the rails sat on pads, known as ‘slab track’. With traditional methods, the use of ballast and sub-ballast is essential as they work together to spread the load onto the subgrade, which must provide sufficient bearing capacity to support the dynamic loads from passing trains. Traditionally, the ballast layer is 300mm thick, with the thickness of the sub-ballast contingent on the strength of the subgrade.
So… what are the main challenges?
Ballast displacement, settlement and degradation
Over time, the subgrade, sub-ballast, and ballast will experience deformation and settlement due to the load cycles they are subjected to, leading to poor track geometry and the loss of vertical and horizontal alignment of the rails. If this is severe, speed restrictions will be implemented which affects day to day operations and profitability. Regular tamping of the ballast and the addition of new ballast can improve alignment, but where the problem lies with a weak subgrade, renewal may be necessary to resolve the issue. Both frequent maintenance and reconstruction options lead to significant disruption to services and incur high costs.
Ballast degradation, or ballast fouling, is the breakdown of coarser grained aggregates, through repetitive loading, into finer particles. Fines build up can lead to significant long-term problems that invariably require remedial works, for example a reduction in load-bearing capacity and drainage capabilities. One of the most significant yet often seen problems caused by this is the development of ‘wet beds’; areas of the trackbed that are consistently saturated with water due to fouled fine particles clogging the voids between larger ballast aggregate, preventing proper drainage. Whilst ballast tamping procedures are used as part of typical trackbed maintenance activities, links exist between an increased frequency of tamping resulting in progressive breakdown of ballast particles/ballast fouling.
Poor trackbed stiffness
Stiffness of the trackbed has a major influence on the overall track system’s stiffness. Track stiffness has a major impact on railway track performance. Some deflection under track loading is inevitable, and this deflection represents a spreading of load, and therefore a reduction of stresses in each layer. However, excessive deflection causes increased stresses in the rail system and dynamic effects on the ballast layer, which in turn leads to loss of track quality. Track geometry, deflections, and longevity are all influenced by the stiffness of the trackbed.
Trackbed stiffness is a composite effect of all support layers and is therefore dependent on the properties and thickness of the ballast and sub-ballast layers, capping or blanket layers, and subgrade.
Trackbed variability
Weak soils present a problem, but variability in subgrade conditions can further exacerbate the likely challenges that will be faced. Variable subgrade creates non-uniform track support conditions. This in turn can result in differential track settlements and loss of alignment, again leading to requirements for extensive, therefore costly and time-consuming, renewal and maintenance work.
Transition zones
Wherever rail track structure changes significantly throughout a route, for example when crossing from a rigid foundation to ballasted track, this is known as a ‘transition zone’. Examples of a rigid foundation would include slab track, culvert, bridge deck, or station slab. In transition zones, the difference in foundation stiffness and settlement gives rise to many challenges for track engineers, including increased stress on track components, dynamic load amplification to underlying structures, differential settlement, and passenger ride discomfort.
Incorporating stabilisation geogrids into trackbed layers to improve performance
In order to maximise efficiency, a rail network must maintain speeds and keep service disruptions for maintenance operations to a minimum. Both the quality and durability of the trackbed are critical, not only in determining the safe operating speeds but also in minimising maintenance-related disruption. When designing the trackbed it is essential to accurately determine the required ballast and sub-ballast thickness to eliminate or mitigate aforementioned problems with subgrade bearing failure, track settlements and ballast degradation under repetitive loading, trackbed variability and smooth ride quality over transition zones.
By designing a trackbed with enhanced bearing capacity and stiffness using a geotechnical solution, such as stabilisation geogrids in the trackbed layers, the time between necessary maintenance can be significantly extended. Additionally, ballast degradation and track settlements are reduced, allowing track speeds to remain high and extending maintenance cycles, saving whole life time, cost, and carbon emissions.
Rail trackbed showing the installation of Tensar TX190L-GN geocomposite (large aperture geogrid with laminated non-woven separation geotextile) for ballast stabilisation over weak ground
Tensar has extensive experience in supporting engineers with designing to meet project specific requirements, ranging from simpler specifications in accordance with national standards to complex Finite Analysis of in-service performance. These research-based methods have been well proven and are now widely used. They deliver financial and sustainability gains and offer improved resilience against the effects of climate change.
Powerful Finite Element Analysis capabilities are possible with the Tensar Stabilised Soil Model (TSSM) plugin
Ballast stabilisation
As previously discussed in this article, repetitive dynamic loading of the ballast layer inevitably leads to ballast degradation, settlements/deformations, and variable levels of performance of the trackbed with regard to stiffness and ride quality, amongst other factors.
Mechanical stabilisation of the ballast layer, typically with a large aperture product to account for the ballast material grading, has been proven to significantly reduce the particle movement and rotation within the zone of confinement of the stabilisation geogrid.
Typical installation location of a ballast stabilisation geogrid
‘SmartRock’ research, presented in 2016, demonstrated the scale of this reduction, using a large aperture Tensar stabilisation geogrid within a ballast layer subjected to cyclic loading. This limiting of translational particle movement heavily reduces degradation and maintains the ballast layer’s strength and drainage characteristics. It also controls ballast displacement, maintaining track alignment and significantly reducing the required frequency of ballast tamping maintenance. Research has shown such extension of the ballast’s life through mechanical stabilisation can extend the maintenance cycle by three times, therefore reducing whole life costs in terms of time, cost, and carbon emissions.
‘SmartRock’ research undertaken demonstrated a significant reduction in particle movement and rotation as a result of the introduction of a mechanical stabilisation geogrid
Below-track structures such as culverts and bridge decks or transition between ballasted track and slab track can create weak abrupt changes in trackbed stiffness that leads to a loss of alignment and poor ride quality that limit track speeds.
Engineered trackbed stiffness is possible across transition zone with stabilisation geogrids (right)
The issue can be addressed by constructing a mechanically stabilised transition zone, incorporating geogrids within either the ballast layer, sub-ballast layer as discussed below, or both, and can provide the ability to design for an engineered variable stiffness. This results in smoother and more durable transitions, improving the overall ride quality, something that the Crew Green Link Road project below benefitted from.
Tensar Case Study: Crewe Green Link Road
A bridge to be constructed across an existing railway embankment, to allow trains to pass over the new Crewe Green Road Link, created the potential for longitudinal differential settlement of the track where it passed between the relatively softer embankment soils and stiffer bridge deck.
Read more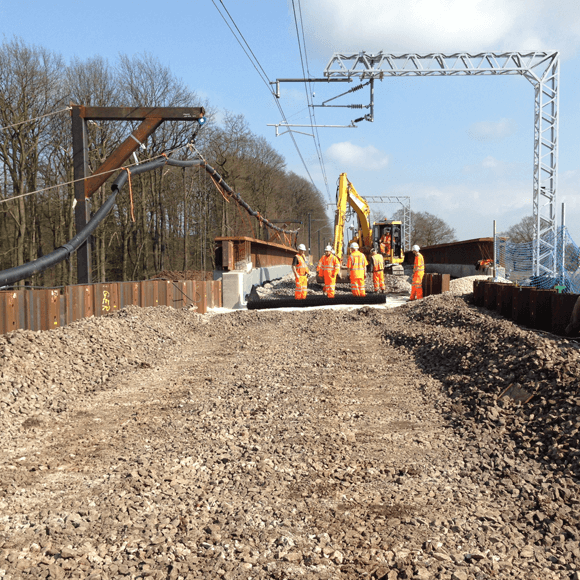
Sub-ballast stabilisation
Soft subgrade conditions lead to an increase in deformation which can affect alignment and may even lead to subgrade bearing failure. The primary function of the sub-ballast layer is to distribute loading over the subgrade to increase bearing capacity, therefore mitigating the risk of bearing failure, and limit subgrade deformation. The weaker the subgrade, the thicker the sub-ballast layer required to achieve adequate distribution.
Therefore, increasing the strength of the sub-ballast or foundation layer through geotechnical solutions increases bearing capacity, reduces settlements, and helps maintain track alignment. One such method of achieving this is to strengthen the sub-ballast layer by incorporating a stabilisation geogrid, typically at the base of the granular material, with additional layers introduced where necessary to ensure continuity of mechanical stabilisation throughout the sub-ballast.
Typical installation location of a sub-ballast stabilisation geogrid
This can enable a considerably thinner sub-ballast layer to be used, saving on the construction costs and need for transportation of expensive aggregates. Single or multiple layers of Tensar geogrid can achieve the required bearing capacity with significantly less sub-ballast material, dependent upon project trackbed performance requirements.
Where variable subgrade conditions arise, track stiffness suffers as a result, leading to uneven settlement and track deflections. Trackbed stiffness has a direct impact on track deflection under load, therefore achieving increased stiffness by mechanical stabilisation of the sub-ballast or foundation layers allows trains to run at higher speeds without shortening the lifespan of the track infrastructure. It can also greatly assist with reducing variability, providing a more consistent track support and therefore an improved ride quality for passengers.
Tensar Case Study: Belfast Transport Hub
Faced with both challenging and variable subgrade conditions and a 5-year contractual zero-maintenance requirement, engineers working on the Belfast Transport Hub project required the undertaking of complex trackbed analysis to ensure that the design assessed the proposed rail loading to an adequate depth of influence.
Read more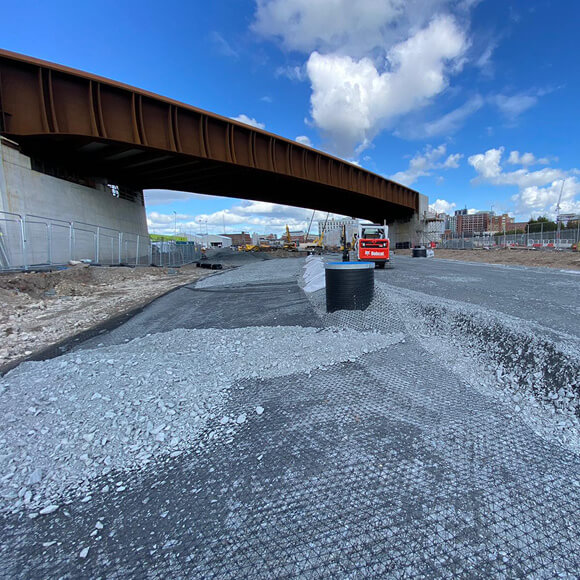
Subgrade improvement
A prepared subgrade, or ‘form layer’, is sometimes adopted on projects above embankment fill material to improve the foundation on which the trackbed layers are to be constructed and therefore must provide adequate bearing capacity to support the sub-ballast and ballast components of the track structure. A frost protection/filtering layer is sometimes specified beneath the sub-ballast, combining with it to form the ‘blanket layers’.
Quality control parameters that are typically ensured during railway embankment construction often include a deformation modulus, or EV2 value, which must be achieved at the top of a prepared subgrade/form layer. The inclusion of a Tensar stabilisation geogrid within this, forming a mechanically stabilised layer, improves the structural performance of the material through increasing particle interlock and reducing movement and rotation, therefore facilitating the use of a thinner layer whilst still achieving the necessary performance characteristics. Alternatively, the same layer thickness can be adopted with the inclusion of a stabilisation geogrid to achieve an increased deformation modulus value. Mechanical stabilisation of subgrade improvement layers can also contribute to maintaining the formation modulus over the lifetime of assets subject to cyclic loading.
In this episode of Ground Coffee Blog, Andrew Lees visits Grand Belfast Central Station. He looks the challenges of building on poor ground conditions and the innovative solution and innovative design method that was used on this project.
Geotechnical solutions for railway embankments
Earth embankments raise the track level above the ground and provide a smooth alignment over undulating ground. Gradually inclined embankments are also required to raise the track level on bridge approaches for river and road crossings. They are an essential component of rail infrastructure, yet railway embankments themselves increase the pressure applied to the underlying ground. The safe height, speed of construction, and long-term settlement will be influenced by the ground properties. Geotechnical engineers will investigate the ground conditions and determine the subsoil properties to be used for the design. Often, without the inclusion of geosynthetic solutions, costly soil replacement is specified, requiring the excavation and replacement of significant volumes of soil material over large lengths of embankment.
In most cases, piling is not required and a geosynthetic reinforced foundation layer will be incorporated to increase bearing capacity and prevent stability failures during construction.
However, where the ground is weak or predicted settlements are high, some form of embankment foundation may be required. In some cases piling or granular columns, such as Geopier Rammed Aggregate Pier® (RAP) system, may be used to overcome weak ground and to eliminate future settlement. This may be in combination with a geogrid reinforced load transfer platform, for example using Tensar Basetex, which can be incorporated to distribute load into the columns.
Tensar Case Study: Green Lane Rail Overbridge Embankment
To minimise the embankment construction footprint for a road bridge over a railway, on a Site of Special Scientific Interest (SSSI), Tensar designed and supplied the TensarTech GreenSlope system.
Read more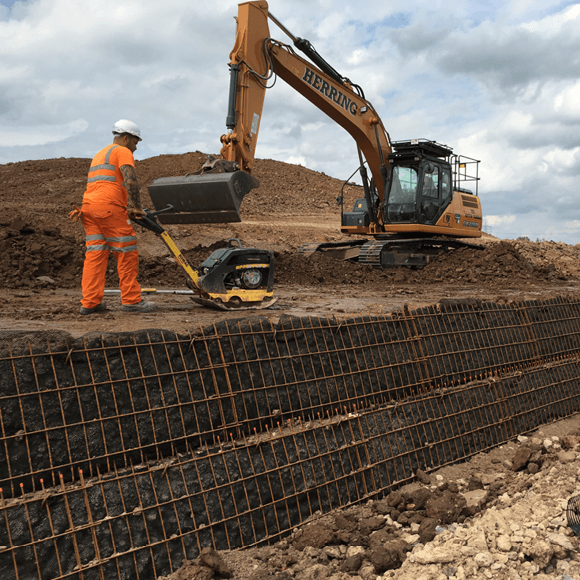
Over very soft soils, a may be installed on the existing ground, often within the embankment itself.
Andrew Lees conducting a simple experiment showing the benefits of a geosynthetic cellular foundation mattress
Such foundation mattress systems have many advantages, including:
- Providing foundation stability without the need for piled foundations or other ground improvement measures
- Elimination or significant reduction of requirements excavation and replacement of soft soils
- Mitigation of an embankment’s typical parabolic settlement profile, instead providing even and controlled settlement
- Allowing faster consolidation and therefore construction timelines
- Supporting access over soft ground for items of construction plant
TensarTech Stratum cellular foundation mattress under construction to support bridge approach embankments in Šenkvice, Slovakia
The use of cellular foundation mattress systems is not limited only to use within embankments for rail infrastructure; Tensar’s Stratum system was used within the Robroyston Link Road project, as detailed below.
Tensar Case Study: Robroyston Link Road
Faced with a 580m stretch of road embankment overlying very weak ground including large peat pockets, a solution was needed to reduce the risk of differential settlement on a new road linking Robroyston Railway Station with the M80 motorway and a large residential scheme.
Read more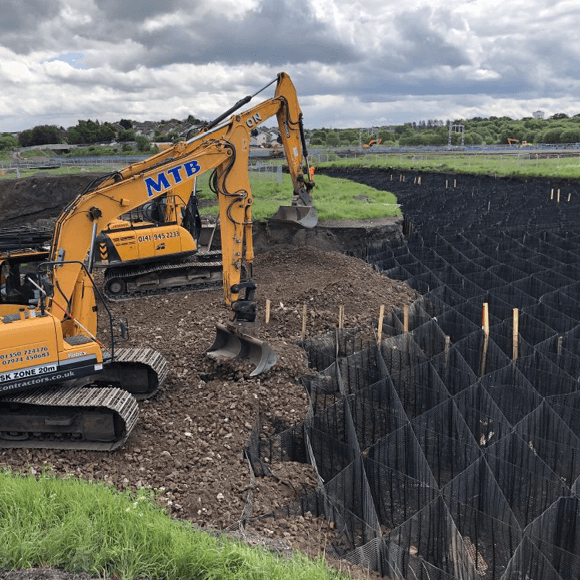
Reinforced soil structures for railways
As railway infrastructure projects face increasingly difficult challenges with construction through topographically ambitious and weak-soiled terrains, increasing train loadings, and an industry drive towards efficiency in whole-life cost, the more traditional methodologies, for example reinforced concrete retaining walls, find themselves up against greater scrutiny.
The following section demonstrates some areas in which reinforced soil solutions might provide a viable alternative.
Improving slope stability – a major railway geotechnical engineering problem
The stability of embankment slopes is crucial for railway engineering. Slow movement of railway embankments will affect track alignment, and total slope failure can close a railway line for many weeks or months. Geotechnical engineers are increasingly frequently needing to deal with risks arising from shallow and complete slope failures. Slope stability is influenced by soil properties, the slope geometry, and by the movement of water. The effects of climate change on rainfall can have a major long-term impact. Fortunately, there are geotechnical engineering solutions to improve slope stability and improve the climate change resilience of railways.
Active shallow slope failures can be halted by stabilising the slope using plate piles, for example using the , an efficient and cost-effective solution for the stabilisation of both new slopes and active slides. The closely spaced Plate Pile elements form a series of horizontal barriers where the soil arches between the plates, forming a continuous line of resistance against downslope movement.
Geopier’s Slope Reinforcement Technology (SRT) system can be installed in-situ to stabilise slope failures
Where slopes have failed, the failed soil can be removed and, in some cases, re-installed with the inclusion of geogrid reinforcement and additional drainage to increase stability and prevent future failures. This approach is quick and avoids the need to transport large quantities of material to and from the site.
Minimising land take using steepened embankment slopes
As embankments increase in height with the same side slope gradient, the base of the embankment must widen, therefore taking up more land. In some cases, this can encroach on existing property boundaries, structures, or infrastructure. One geotechnical engineering solution can be to increase the gradient of the embankment side slope, though steepening a slope reduces internal stability and can lead to rapid slope failure.
A commonly used geosynthetic engineering solution is to design the slope as a reinforced soil structure. By incorporating layers of geogrid, the internal stability is increased. Railway embankment slopes may be constructed at angles of up to 70° using this technique. Tensar has two solutions for steep slope construction. – TensarTech Greenslope for slopes up to 70° and TensarTech NaturalGreen for shallow slopes up to 45°.
One such use of these systems was on the Murrayfield Stadium Tram Stop project, in Edinburgh, where a combination of Tensar’s GreenSlope and TW3 block wall reinforced soil structures were used.
Tensar Case Study: Edinburgh Tram Link
Tensar’s reinforced soil solutions enabled lightweight expanded clay aggregate fill to be used to build the reinforced soil structures between bridges that carry the tram route over roads and a river.
Read more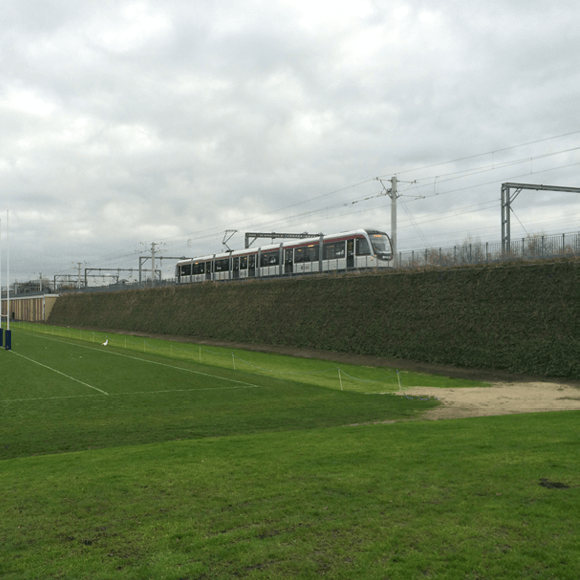
Retaining wall systems for railways that are quicker and cheaper to construct
Earth retaining walls are fundamental to rail infrastructure, acting as both track side protection and support for elevated tracks. Retaining walls in the context of railways are especially important where grade separation is required in spatially constrained areas, for example in high-density urban cities.
In the past, retaining walls would typically be constructed from steel piles, masonry, or reinforced concrete gravity walls. The latter two both require substantial foundations, requiring piling or excavation. Today, railway geotechnical engineers are able to adopt geosynthetic solutions, such as geogrid reinforced retaining walls. These systems use reinforced soil techniques to create stable retaining walls that are economical, quicker to construct and lower embodied carbon. In some cases, no foundation works are required, and site-won/marginal fill may be utilised for the structure, greatly reducing local impacts from construction activities.
Much of the existing railway infrastructure was built in the nineteenth century. Masonry walls may need upgrading or replacing to cope with modern railway loading. Railway geotechnical engineers have used reinforced soil systems constructed behind existing walls, designed to relieve thrust onto the ageing structures. In a similar application on the Bermondsey Dive Under project, reinforced soil retaining wall structures were used to support rail loading on the approach structure tie-ins to masonry arch structures.
Railway geotechnical engineering solutions for earthworks and bridgeworks
Almost all rail projects involve major earthworks and the construction of structures such as bridge abutments and retaining walls. Railway geotechnical engineers, faced with difficult terrain and soft or variable ground conditions, are seeking solutions that offer best value at the time of construction as well as durability and resiliency.
Tensar has innovative solutions for all geotechnical challenges arising from railway structures such as bridges and embankments over weak soils, with faster construction, reduced land take, and controlled settlements, for a longer lasting, optimal value, resilient infrastructure.
Tensar Case Study: Falahill Borders Railway
When building a bridge carrying the A7 road over the new Borders Railway, Scottish Borders Council’s construction arm, SBc Contracts, were seeking a cost-effective alternative to concrete panel faced wing walls.
Read more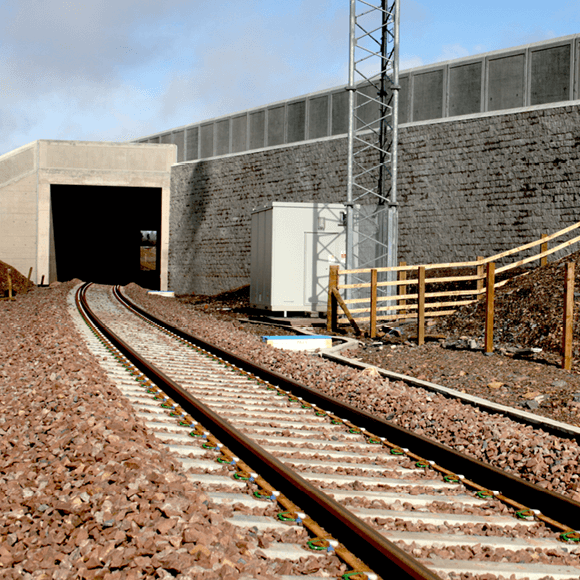
Efficiency in design and construction of temporary works that support railway infrastructure projects
Railway infrastructure projects will invariably involve a requirement for enabling or supporting works, often categorised as “temporary works”, to facilitate the construction of permanent structures.
Traditionally adopted design methodologies can lead to inefficiencies within temporary works design, giving rise to often unforeseen and extensive costs in construction material and time requirements, and a resultant increase in risk profile of the activities to be undertaken. Mechanical stabilisation of quarried aggregates can provide Consultants, Contractors and Clients with safe, extensively validated, and independently peer-reviewed alternative design approaches. For example, Tensar's T-Value working platform design methodology can offer the benefit of significant reductions in construction cost, build time, and carbon emissions, through reductions in the required quantities of aggregate material.
Tensar’s T-value methodology, alongside other design approaches for typical temporary works site requirements, can be used on Tensar’s award-winning, free to use, cloud-based construction design software, Tensar+. Users can generate mechanically stabilised designs with standard input parameters and quantify comparative value for reductions in construction time, cost, and carbon emissions vs non-stabilised alternatives, adopting market values appropriate to the user’s region and application.
Tensar has extensive experience of providing temporary works solutions to projects, often on schemes with critical rail interfaces and complex engineering challenges. Whether a project requires site compounds, access roads, working/piling platforms, or temporary load bearing bridge abutments, Tensar can assist across the full spectrum of application areas. View Tensar's Next Generation solutions flyer to find out more.
Tensar Case Study: HS2 Stoneleigh Park working platform
As an alternative to traditional design methods, a leaner working platform was required for the Stoneleigh Park Overbridge piling operations, which needed to address the issues of high rig track pressures over a weak and variable subgrade.
Read more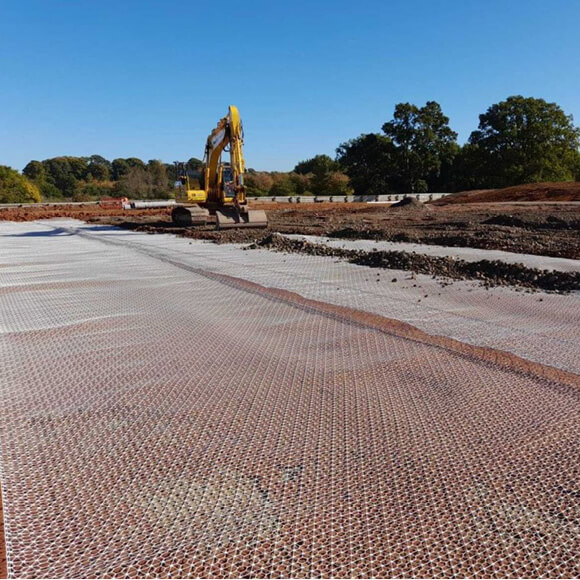
The Tensar difference
Tensar offers proven, high-performance geosynthetic solutions for railway geotechnical engineering that enable you to deliver your project with confidence. Not only do they provide significant value and sustainability benefits over alternative solutions, but they’re also widely accepted by rail authorities worldwide and have had their performance proven and quantified by extensive research and field trials.
Our range of geosynthetic solutions for railway embankments and rail trackbed reinforcement includes:
- Tensar® InterAx® (NX) Geogrids
- Tensar® TriAx® (TX) Geogrids
- Tensar® TriAx® (TX-G) Geocomposite
- Tensar® Biaxial BX Geogrids
- TensarTech® Stratum® Cellular Foundation Mattress System
- Tensar® Basetex® Geotextile
- TensarTech® TW1 Wall System
- TensarTech®TW3 Wall System
- TensarTech®TR2 System
- TensarTech® RockWall™ Rock Cage Retaining Wall System
- TensarTech® NaturalGreen™ Slope System
- TensarTech® GreenSlope System
- Tensar® Basetex® Geotextile
Have an upcoming rail project and require expert support? our design team are here to help.
Get in touch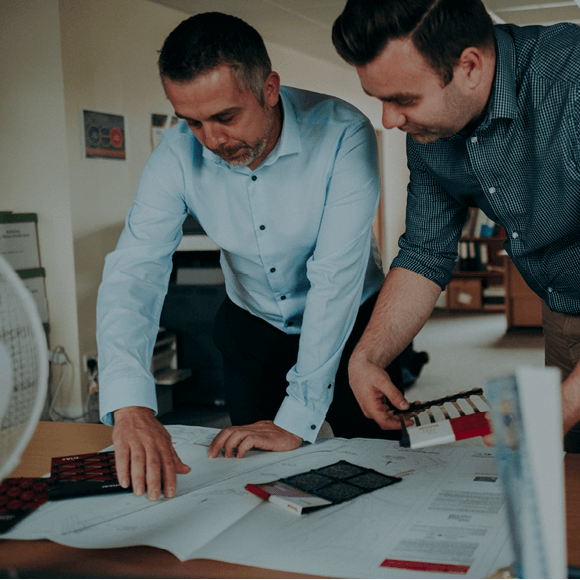