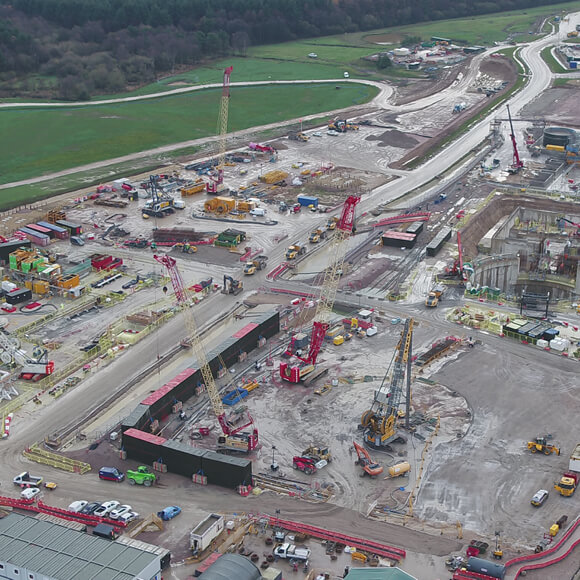
Working Platform Design
A unique design approach & software specifically for stabilised working platforms
Safety is critical when using mobile cranes, piling rigs and other heavy plant machinery on construction sites, particularly over weak and variable ground. Storage areas for plant machinery and materials on site need to be smooth, clean and free of ruts, so safe working platform design is essential.
Tensar geogrids can be incorporated in the granular material to stabilise working platforms and increase bearing capacity, limiting surface deformation and settlements. Strengthening the granular layer enables the working platform thickness to be reduced. By reducing the volume of fill required, costs, time and emissions are reduced, contributing to sustainability objectives.
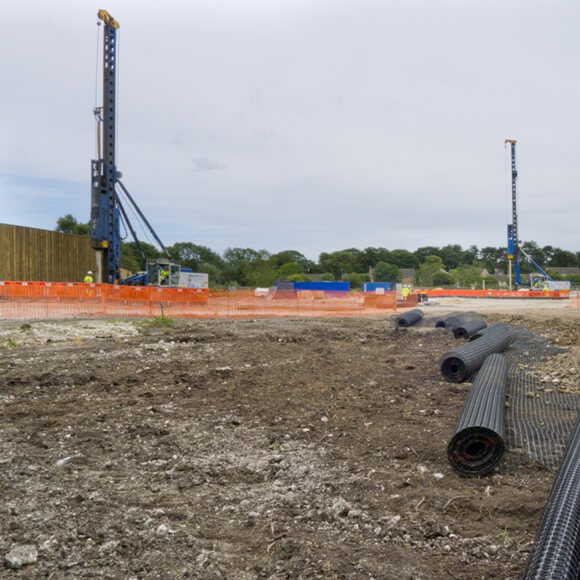
How does Tensar geogrid improve working platform strength?
The interlocking mechanism and particle confinement that develops between the aggregate and the Tensar geogrid, prevents lateral movement of the granular material. This creates a mechanically stabilised layer that significantly increases bearing capacity, and controls differential settlement.
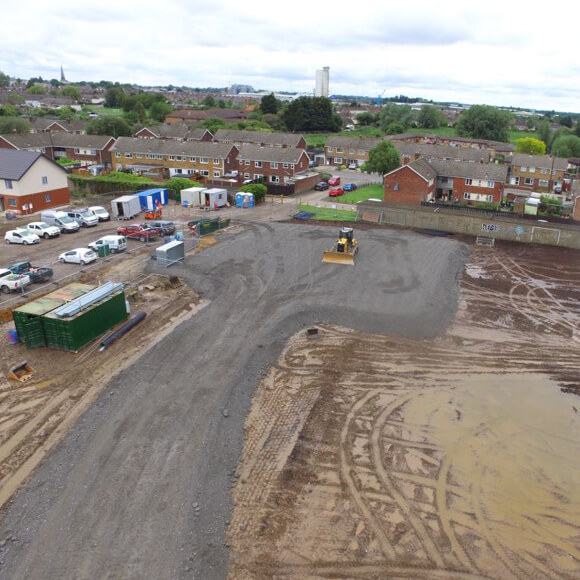
The importance of investigation
Working platform design should be carried out by a competent, geotechnical engineer. Design depends on ground conditions and requires sufficient ground investigation data. Platform thickness depends on subgrade strength, the platform materials and, of course, the expected construction loads. It is important to have a platform that can provide sufficient bearing capacity for safe working, while being economic and straightforward to construct.
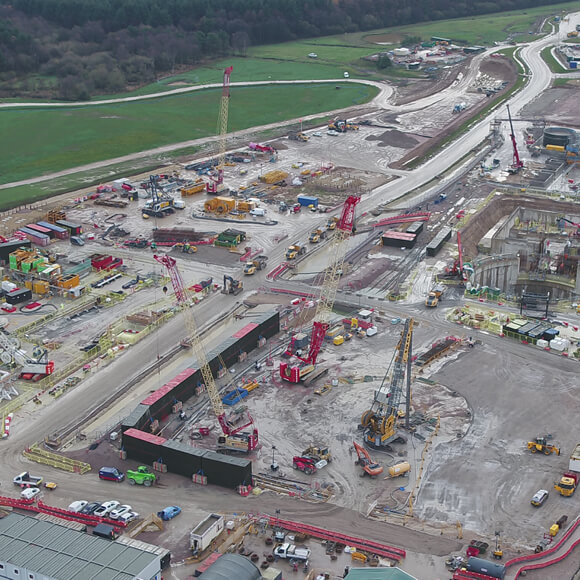
T-Value Method of Calculation
Tensar’s T-value method enables a more accurate assessment of the positive effect of stabilising geogrids, on the bearing capacity of a granular working platform. Applicable to a range of working platform materials, in different ground conditions, the method enables designs with, or without, geogrid to be compared - including for subgrade soils with very low shear strength. It can also be applied to surface and shallow embedded foundations, with dry or saturated granular layers.
For the first time, the full benefits of stabilising geogrids can be incorporated consistently in designs for working platforms. The T-Value method delivers verifiable designs that can reduce platform thickness and improve bearing capacity, cutting construction costs by up to 30% and reducing a platform’s carbon footprint by up to 40%.
The benefits of working platform stabilisation
Using Tensar geogrids to create a mechanically stabilised aggregate layer (MSL) has significant benefits over non-stablised aggregate working platforms:
- Increased bearing capacity: the mechanically stabilised layer has an increased bearing capacity, creating a safer and more reliable working platform design for the operation of heavy plant and machinery.
- Reduced layer thickness: the aggregate layer can be reduced by more than 50% with no performance loss. This may also mean that less subgrade soil needs to be excavated and disposed of.
- Lower quality and recycled aggregate fill: With increased layer performance, the use of a Tensar MSL may enable the use of lower quality fill materials such as reclaimed aggregates.
- Long-term cost savings: less excavation and use of reclaimed aggregates can reduce construction costs and site CO2 emissions.
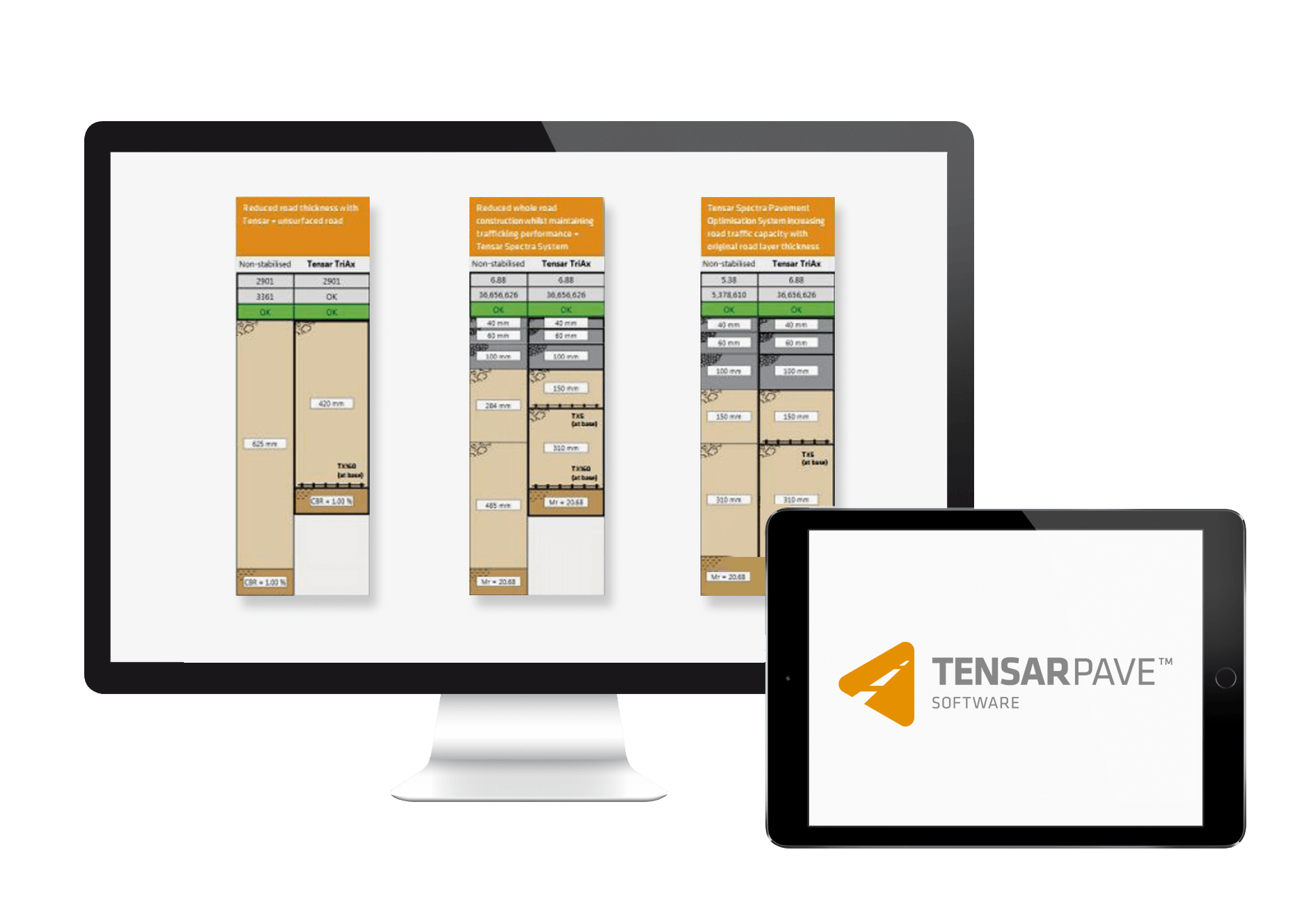